Laser Welding
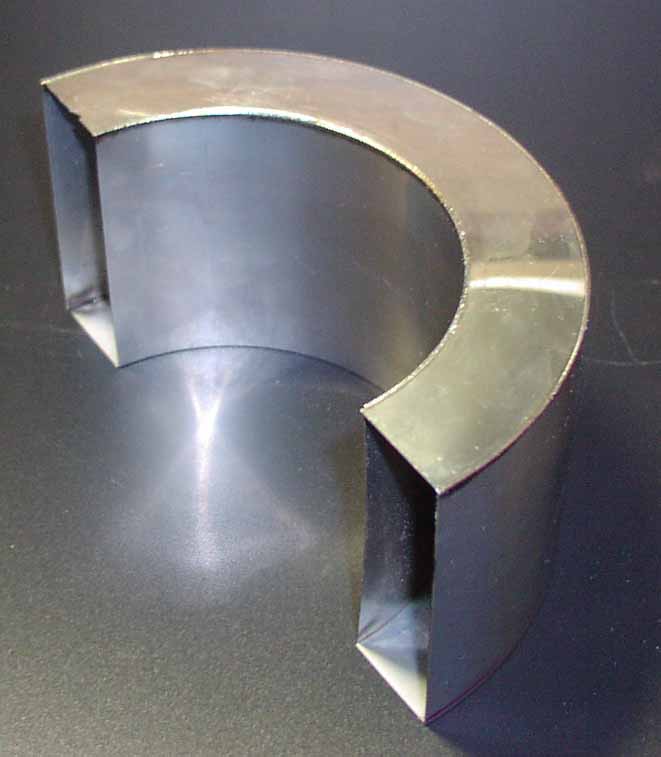
Laser welding is one of the most effective welding processes:
- efficiency approximately 25%;
- no consumable items or materials;
- low operational costs;
- minimum dimensions;
- total operation time of minimum 100 000 h.
Fibre laser welding increases welding speed by approximately 50% for steels and up to 80% for aluminium alloys. Combined
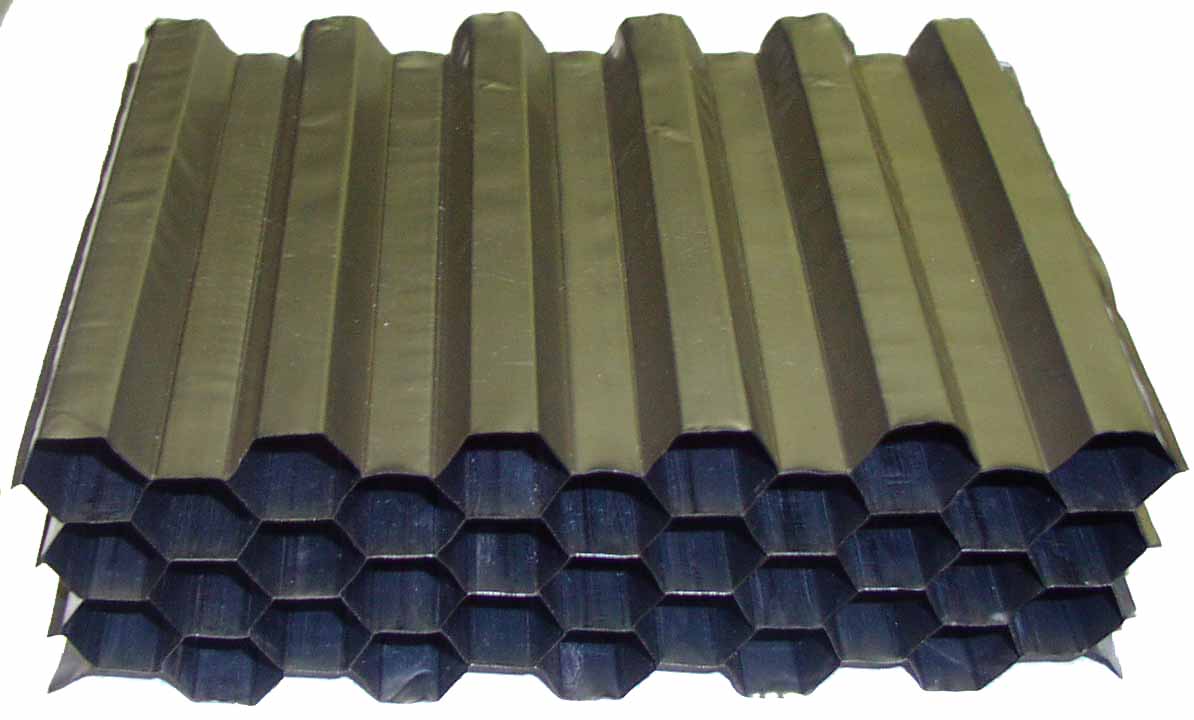
Depending on laser power with use of one welding tip it is possible to weld metals of different thickness and hardness, plane, curvilinear and multilayer structures without deformation, structures like «
The laser welding is effective not only in mass production, but also in manufacture of unique items. Characteristics of items most appropriate for laser welding:
- shell content cannot be exposed to heating;
- permissible thermal deformations after welding are very small or within close tolerance;
- powerful magnets in structure;
- heterogeneous metals to be welded;
-
thin-walled element to be welded to massive one; - welding inside (in the recess) the assembly.